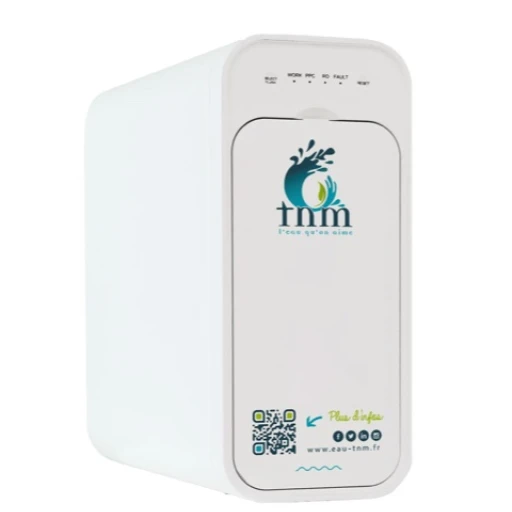
Comprendre la transition numérique
Le tournant numérique dans le secteur industriel
La transition numérique dans l'industrie représente une transformation profonde et essentielle pour rester compétitif dans un marché en constante évolution. Cette mutation ne se limite pas simplement à l'adoption de nouveaux outils technologiques comme les tours numériques ou les centres d'usinage CNC, mais implique une démarche globale où chaque technique, chaque processus est réinventé à la lumière des possibilités offertes par le numérique. La mise en place d'un affichage numérique au sein d'une usine, par exemple, permet d'améliorer significativement la précision des mesures et le suivi des performances des machines. Les tours CNC et les mandrins de tour sont équipés de dispositifs de serrage et d'une vitesse de broche ajustable pour maximiser l'efficacité du processus de tournage. Mais ce n'est qu'une partie de la transformation numérique. Les pièces usinées à l'aide de ces technologies tirent parti d'un contrôle précis sur chaque axe, permettant une meilleure adaptation aux demandes spécifiques des clients, que ce soit pour le tournage de métaux, de bois ou d'autres matériaux industriels. L'impact de la vitesse de broche principale et des dispositifs d'alésage de broche sur la qualité et la rapidité de production ne doit pas être sous-estimé. Pour mieux comprendre les complexités et l'importance de cette transition numérique, il est crucial de se pencher sur le rôle des génératrices tachymétriques modernes, une composante essentielle des machines outils actuelles, comme expliqué dans ce guide détaillé sur les génératrices tachymétriques. L'intégration de technologies numériques offre également de nouveaux moyens pour les industries de répondre aux défis contemporains. C'est une évolution inévitable pour toute entreprise souhaitant rester pertinente dans un avenir industriel de plus en plus digitalisé.Les technologies clés de la tour numérique
Les technologies phares soutenant la transformation numérique
Dans le contexte de la numérisation industrielle, plusieurs technologies jouent un rôle central pour révolutionner les méthodes de fabrication traditionnelles. Parmi celles-ci, les outils numériques tels que les tours CNC, véritables bijoux de précision, sont en première ligne. Les tours numériques, équipés de dispositifs de serrage et de broches principales à haute vitesse, permettent des opérations d'usinage complexes sur différentes pièces métalliques et en bois. Leur affichage numérique avancé garantit une précision inégalée dans les processus de tournage, avec des axes multiples rendant possible un usinage multi-dimensionnel et une supervision en temps réel des performances. Les machines-outils modernes intègrent également des technologies de ravitailleur de barres, optimisant ainsi le flux de production et réduisant les temps morts. Cela permet aux industriels de maximiser la capacité des tours verticaux dans le cadre de centres de tournage avancés. Le centre d'usinage CNC devient ainsi un pilier pour des industries cherchant à améliorer l'efficacité et la précision de la production. En sus, l'automatisation des tours, grâce à des dispositifs avancés de serrage et des outils de coupe de pointe, facilite le traitement polyvalent des matériaux tout en garantissant la sécurité et la réduction des erreurs humaines. Pour une compréhension approfondie de ces défis et opportunités, la popularité croissante des drones dans l'industrie agricole offre un aperçu pertinent de l'impact des technologies numériques sur divers secteurs industriels.Les avantages de la numérisation industrielle
Les bénéfices incontournables de l'industrialisation numérique
La transition vers la numérisation a permis à l'industrie de bénéficier de nombreux avantages qui transcendent le simple cadre de la production. En intégrant les technologies numériques, les entreprises industrielles peuvent atteindre une plus grande efficacité, précision et compétitivité sur le marché mondial.- Optimisation des processus de fabrication : L'utilisation de machines-outils numérisées, telles que les tours CNC et les centres d'usinage, permettent une production plus rapide et précise. Grâce à ces outils, les composants sont fabriqués avec une précision accrue, influençant directement la qualité des pièces produites.
- Amélioration de la précision et de l'efficacité : Les dispositifs de serrage avancés, ainsi que les fonctions d'affichage numérique, permettent aux opérateurs de garder un œil sur toutes les variables de l'usinage telles que la vitesse de la broche et l'axe de tournage. Cela minimise les erreurs humaines tout en augmentant la productivité.
- Réduction des coûts opérationnels : L'intégration intelligente des technologies numériques entraîne une réduction des coûts en rationalisant les opérations. Les ressources sont allouées de manière plus efficace, diminuant ainsi les gaspillages.
- Flexibilité et adaptabilité accrues : Les machines telles que le tour numérique et le ravitailleur de barres facilitent la gestion des changements dans la production. Ces machines permettent de s'adapter rapidement à des spécifications différentes sans nécessiter de configurations complexes.
Défis et obstacles de la transition numérique
Obstacles techniques et organisationnels
La transition numérique dans l'industrie n'est pas sans défis. Les entreprises doivent souvent faire face à des obstacles techniques liés à l'intégration de nouvelles technologies comme les tours numériques et les machines CNC. Ces outils, bien que prometteurs en termes de précision et d'efficacité, nécessitent une mise à jour des compétences des opérateurs et un investissement conséquent en formation. Les dispositifs de serrage, la vitesse de broche, et l'affichage numérique sont autant de paramètres à maîtriser pour optimiser l'usinage des pièces.
Coût et retour sur investissement
Le prix des équipements numériques, tels que les centres d'usinage et les tours CNC, représente un frein majeur pour de nombreuses entreprises. Le retour sur investissement n'est pas toujours immédiat, surtout si l'on considère les coûts d'installation et de maintenance des machines outils. Les industriels doivent évaluer avec soin les bénéfices à long terme par rapport à l'investissement initial.
Résistance au changement et gestion du personnel
Un autre défi crucial est la résistance au changement au sein des équipes. L'introduction de nouvelles technologies peut générer des inquiétudes parmi les employés, notamment en ce qui concerne la sécurité de l'emploi et l'évolution des compétences requises. La gestion du personnel devient alors un enjeu stratégique, nécessitant une communication claire et une formation adaptée pour accompagner cette transition.
Intégration et interopérabilité
L'intégration des nouvelles technologies avec les systèmes existants pose également problème. Les tours numériques et les machines CNC doivent pouvoir s'intégrer harmonieusement dans les processus de production déjà en place. Cela nécessite souvent des ajustements complexes pour assurer l'interopérabilité entre les différents dispositifs, comme les mandrins de tour et les broches principales.
En somme, bien que la transition numérique offre de nombreuses opportunités, elle exige une préparation minutieuse et une gestion rigoureuse des défis qui l'accompagnent. Les entreprises doivent être prêtes à investir non seulement dans des technologies avancées, mais aussi dans le développement des compétences de leur personnel pour réussir cette transformation.
Études de cas : succès et échecs
Exemples de réussites et d'échecs dans la transition numérique
La transition numérique a apporté des transformations majeures dans l'industrie, avec des exemples de succès retentissants mais aussi des échecs notables. Analysons quelques cas qui illustrent ces dynamiques.
Succès : L'intégration des tours CNC dans l'usinage
Les tours CNC ont révolutionné l'usinage des métaux grâce à leur précision et leur efficacité. Des entreprises ont su tirer parti de ces machines pour améliorer la qualité de leurs pièces tout en réduisant les coûts de production. L'adoption de ces machines-outils a permis une flexibilité accrue dans la production, notamment grâce à la capacité de changer rapidement de mandrin ou de broche pour s'adapter à différents axes et procédés de tournage.
Échec : L'implémentation hâtive de dispositifs numériques
À l'inverse, certaines entreprises ont échoué en tentant d'implémenter des technologies numériques sans préparation adéquate. Par exemple, l'introduction précipitée de systèmes de vitesse de broche avancés sans formation appropriée a entraîné des arrêts de production et des coûts imprévus. Ces erreurs soulignent l'importance d'une planification rigoureuse et d'une formation continue lors de la transition vers des machines numériques.
Leçons apprises
- Formation continue : Une formation adéquate est essentielle pour maximiser l'efficacité des nouvelles technologies.
- Investissement stratégique : Investir dans des tours numériques et autres outils doit être basé sur une analyse approfondie des besoins spécifiques de l'entreprise.
- Planification : Une transition numérique réussie nécessite une planification minutieuse pour éviter les interruptions de production.
En somme, la transition numérique dans l'industrie, bien qu'elle présente des défis, offre d'énormes opportunités pour ceux qui savent l'aborder avec stratégie et préparation.
L'avenir de l'industrie à l'ère numérique
Perspectives d'évolution et innovations émergentes
La transition numérique continue de transformer profondément l'industrie, ouvrant la voie à de nouvelles possibilités. Voici quelques axes d'évolution majeurs dans le cadre de l'industrie numérique :- Iot et Big Data : L'intégration de capteurs intelligents sur les machines outils comme les tours numériques offre une collecte de données en temps réel. Ces informations facilitent la maintenance prédictive et optimisent l'utilisation des ressources, améliorant ainsi la productivité.
- Intelligence Artificielle : L'adoption de l'IA dans des dispositifs tels que le centre d'usinage permet d'améliorer la précision et l'efficacité du processus de tournage. Les broches et mandrins actuels bénéficient d'ajustements automatiques, réduisant les erreurs humaines.
- Automatisation avancée : L’ère numérique voit une montée de l'automatisation avec des tours CNC équipés de ravitailleurs de barres permettant un flux de production ininterrompu. Cette automatisation réduit les temps d'arrêt et améliore les cadences de production.
- Fabrication additive : La combinaison de l'usinage traditionnel et de la fabrication additive positionne l'industrie sur un nouveau plan d'innovation, permettant la fabrication de pièces industrielles complexes impossibles à réaliser auparavant.
- Cyber-sécurité : Avec l'intégration croissante des technologies numériques, les défis de la sécurité prennent une importance incontournable. Protéger les données industrielles est aujourd'hui crucial pour assurer la continuité des opérations.